by Mark Bowling, Level II Thermographer, IRISS Inc.
Overview
The installation of infrared windows into electrical distribution equipment is
an excellent way to kick-start a Condition-Based Maintenance (CBM) Program.
Standard round and rectangular IR windows are available to suit most applications on
switchgear, switchboards, MCCs, transformers, drives, etc. However, some
equipment types like panelboards can be very difficult to retrofit standard sized IR
windows at all due to their unique construction. Panelboards are very compactly
designed and in order to perform a proper IR inspection, the dead-front covers
typically need to be removed while equipment is energized and under normal load
conditions. To do this safely, PPE must be worn and a 2-3 man crew will be required
for at least 2 hours per panelboard. In addition, many customers have very limited
downtime available to actually perform the IR window install which involves
punching, drilling, cutting, touch-up painting, panel removal and re-installation. In
these instances, custom replacement panels can both minimize installation time and
also allow the design of custom window sizes and locations that would otherwise not
be possible.
IRISS channel partner Connected Power of Lakeland, Florida recently engaged with a
client with these exact issues. The client, a renowned leader in aerospace fluid
management and filtration solutions, had a power distribution system comprised of
Schneider Electric / Square D switchgear, panelboards and transformers. They were
uncomfortable performing energized open panel inspections but recognized the value
of doing regular infrared scans of their equipment. It had already been determined by
Connected Power personnel during a preliminary site visit that standard windows
would not work on the panelboards, dry transformer, main distribution panel and main
switchgear breaker section at the site. The client’s facility operates 364 days per year
and had their one shutdown day coming up and it was decided to dispatch the IRISS
3D scanning team to gather the necessary data to design and build custom panel
solutions for the client.
So, on a sunny Sunday last fall, the team from IRISS traveled to the client’s site
on the day of the annual shutdown. The critical equipment panels were removed,
dotted with 3D scanner targets, and using a Creaform HandySCAN 700 handheld 3D
scanner, the existing panels were digitally recorded. Upon returning to the office,
IRISS mechanical designers uploaded the 3D files and converted them to CAD. The IR
windows, doors, latches and retaining hardware were added in the appropriate
locations to the base panel CAD drawings, and then part drawings were uploaded
to our CNC turret press for manufacturing. Paint colors were matched to the OEM’s
standards on each equipment type to ensure the replacement panels would look like
they had come from the factory with the IR windows already designed in place. The
fully vertically integrated manufacturing operations at IRISS ensured all the work was
done in-house in our Bradenton, Florida factory.
Three weeks after placing the order, the client received six (6) custom panels for field
replacement. Field replacement was done in a matter of minutes on each piece of
equipment. The client can now safely perform infrared inspection on all of his
equipment while keeping it in a closed and guarded condition. In situations where
equipment panel drawings cannot be sourced from the OEM, the 3D scanning
capability and advanced manufacturing resources of IRISS can still ensure a viable
solution for the client.
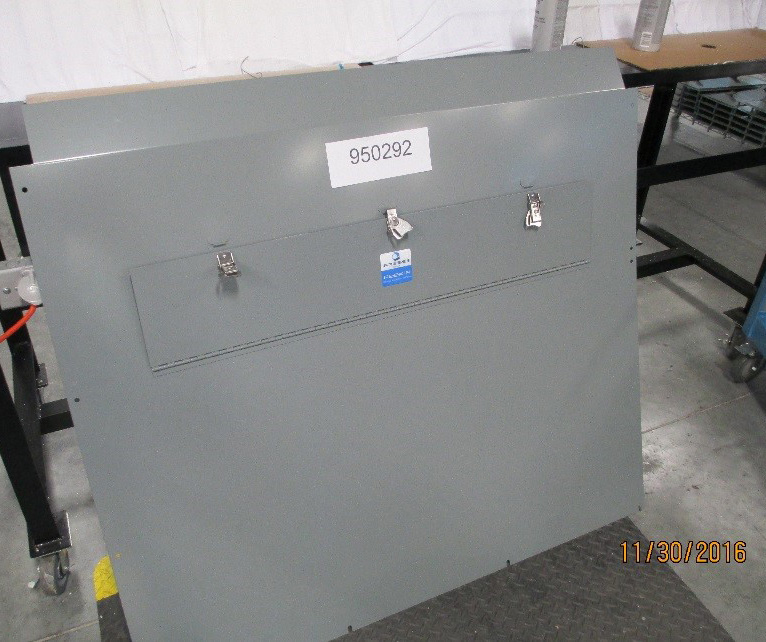
Figure 1 Custom Replacement Panel for Dry Transformer
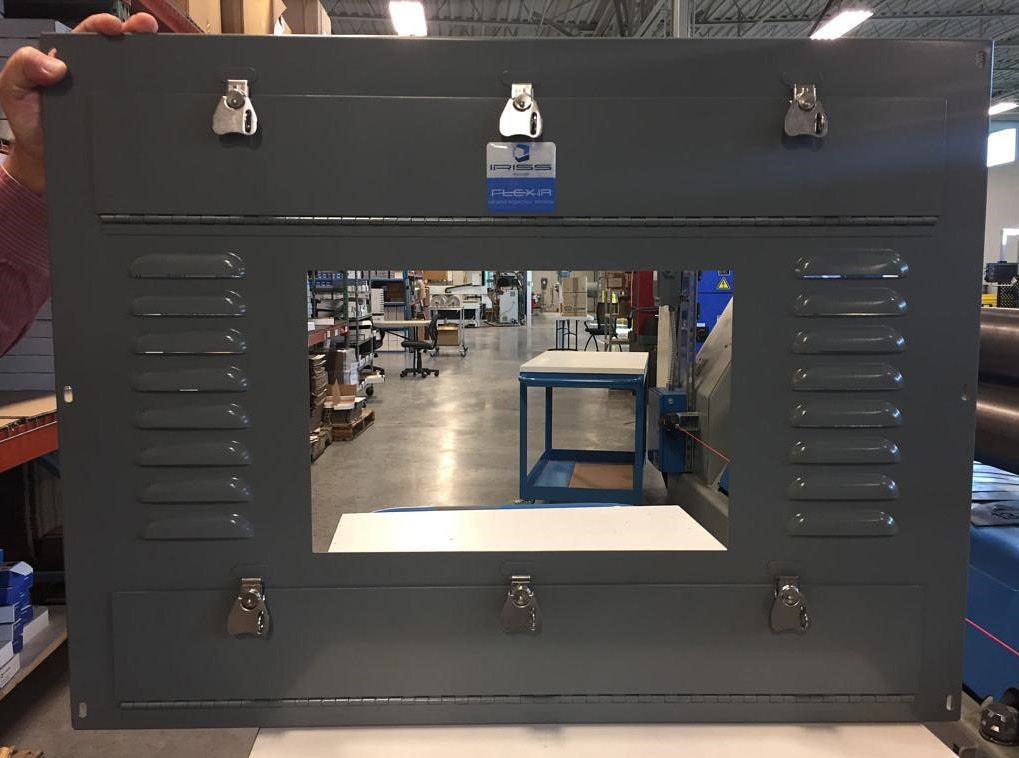
Figure 2 Replacement Ventilated Panel for Switchgear (IR Windows to Scan Line and
Load Side Connections of Main Breaker)
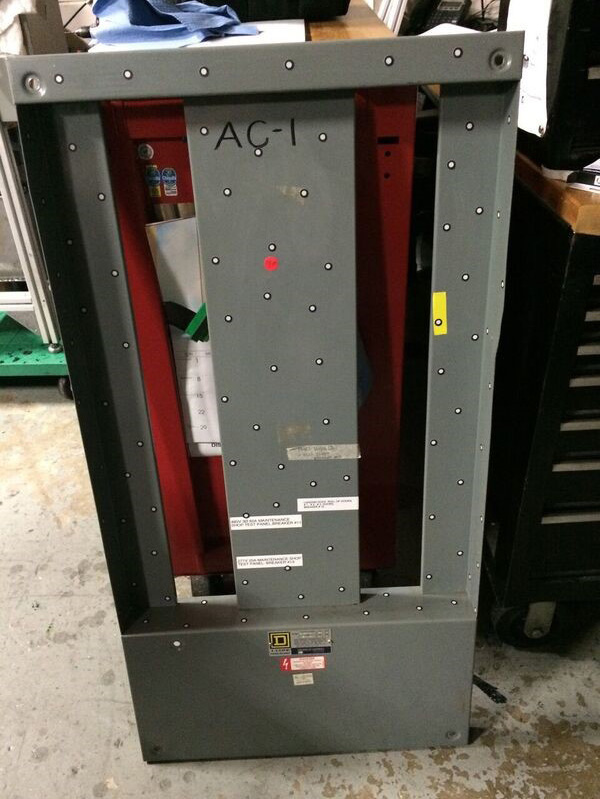
Figure 3a Panel AC-1 Prepped for 3D Scanning
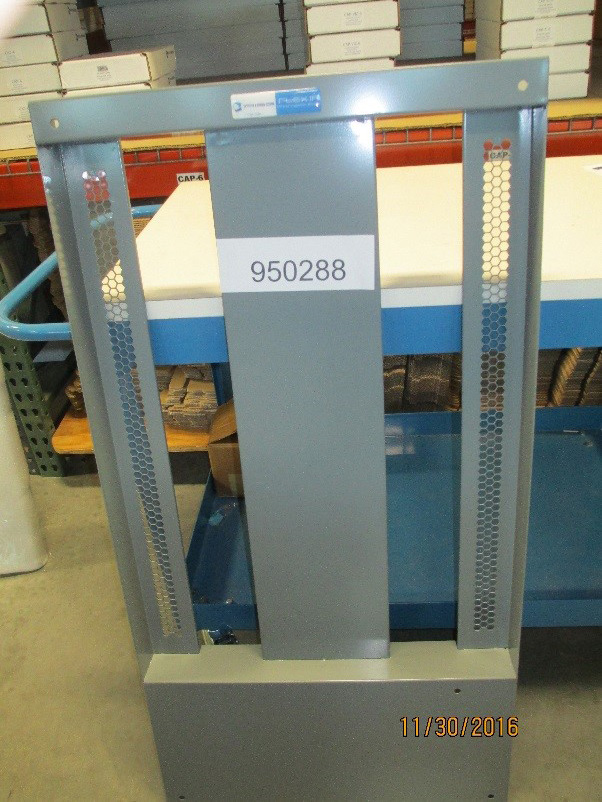
Figure 3b Panelboard Deadfront Replacement for Panel AC-1 with IR
windows to Scan Load Side Connections of Feeder Breakers
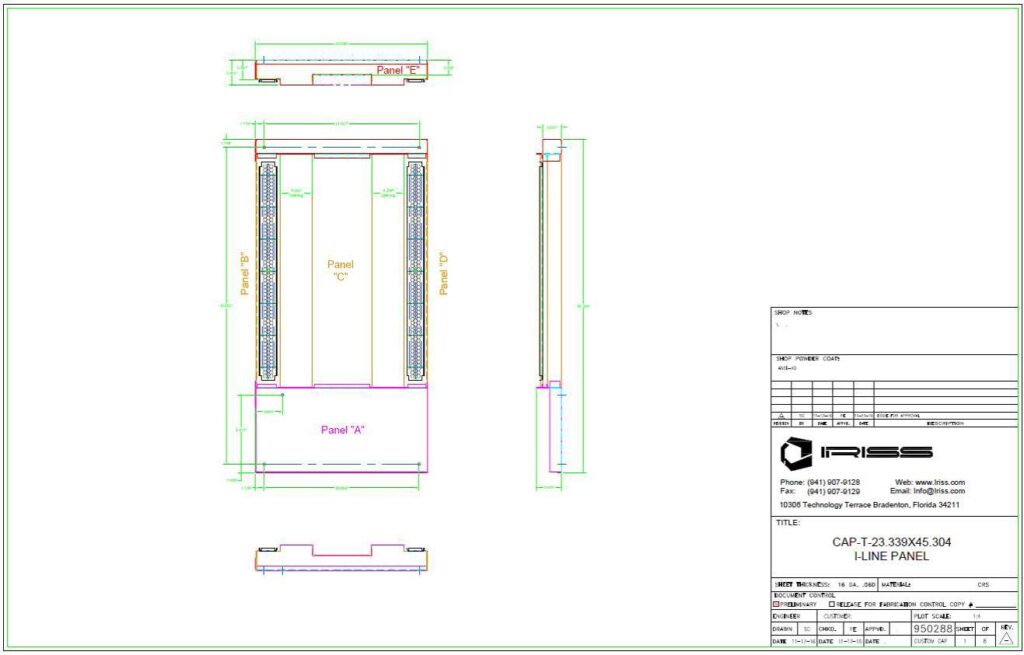
Figure 3c CAD Drawing for Panelboard Deadfront Replacement for Panel AC-1
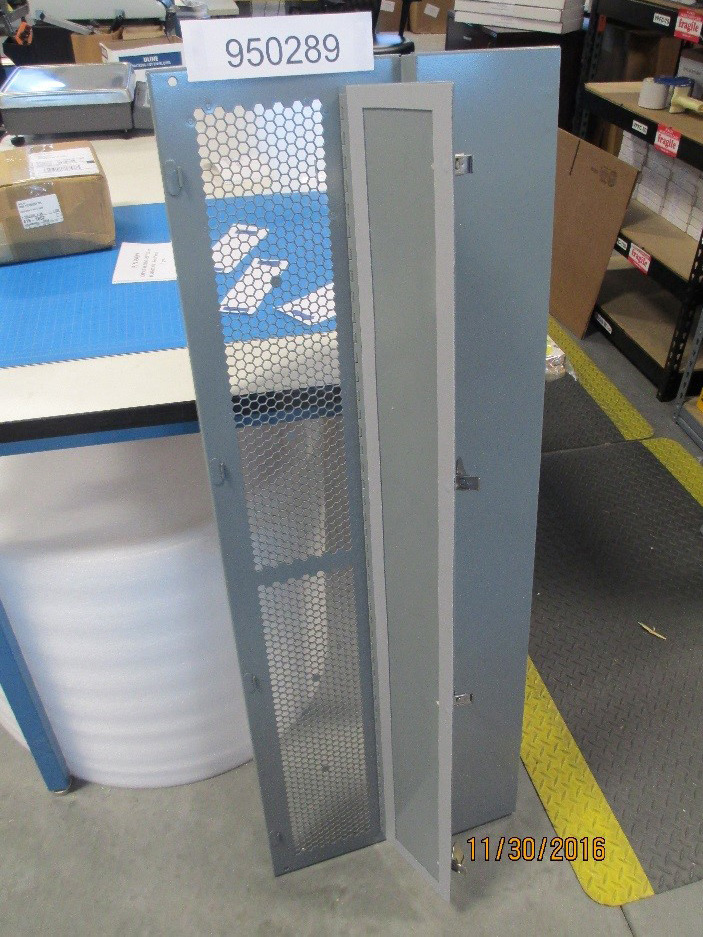
Figure 4 Main Distribution Panel (MDP) Gutter Cover with IR Window for Load Side
Feeder Breaker Inspections