by Jason Bricker, Level 1 Thermographer, IRISS Inc.
Overview
Recently, the chief electrician of a large offshore drilling company realized the
problems his staff were having performing safe and efficient infrared inspections on
their electrical equipment. In order to comply with the corporate safety policy for
mandatory inspections on the drillship, he hired multiple consultants to explore
faster and safer alternatives. Ty Keeth, Level III Thermographer, IRISS Certified
Installer, representing Offshore Inspection Group, was from one of the companies
attempting to solve the problem.
After Ty analyzed the electrical equipment on the drillship, he quickly realized that
there were only visual viewing windows and no sign of any infrared inspection
windows. According to Ty, “There are a unique set of problems on a drillship with the
main concerns being the safe and reliable operation of power distribution assets on
the ship. It is a major undertaking to turn off equipment.” As a result, any inspections
take a considerable amount of manpower and time.
At the time Ty was contacted, the process for one inspection involved:
- Preplanning stage to identify the equipment and obtain approval to shut down.
- De-energizing the equipment required two electricians to make sure it was safely
isolated, locked out and tagged out. - Once de-energized, the two electricians removed all covers for inspection on the
equipment in question. - Once the covers were removed, approval to re-energize and operate the
equipment was obtained, and locks and tags were removed. - Appropriate PPE was put on by the electricians, and the equipment was reenergized.
- Together with operations, the electricians confirmed the equipment was operating
at normal load levels and allowed sufficient time for the equipment to become
thermally stable. They then performed an infrared inspection of the equipment. - Personnel then completed the inspection, taking any notes of problems
discovered. - Electricians de-energized the equipment again following lock-out, tag-out
procedures and, when safe, put the equipment panels back in place. - Finally, electricians re-energized the equipment.

With this complex process, the time involved in performing an inspection on
one electrical asset was between four to six hours.
The drillship had six thruster transformers, six mud transformers, six drilling
transformers and 66 high-voltage switchgear cabinets. There were approximately 30
different types of equipment needing to be inspected. Due to the volume, the existing
inspection process took three to five people between two to three weeks to perform.
Another consulting firm suggested that standard 6-inch IR windows be installed in
front and back of the heavy switchgear equipment, but this would require multiple
significant modifications to the existing panels that would be both time-consuming
and could jeopardize the enclosure integrity.
The better solution was proposed by Ty Keeth. He took the time to analyze how
the IRISS FlexIR Custom Windows could be a bespoke design to require negligible
enclosure modifications and save the company both on installation labor and IR
window procurement cost. He was able to accomplish this by replacing the existing
visual viewing windows in the switchgear with the IRISS FlexIR Custom Windows that
allow both infrared inspection and visual inspection through the clear reinforced
polymer optic.
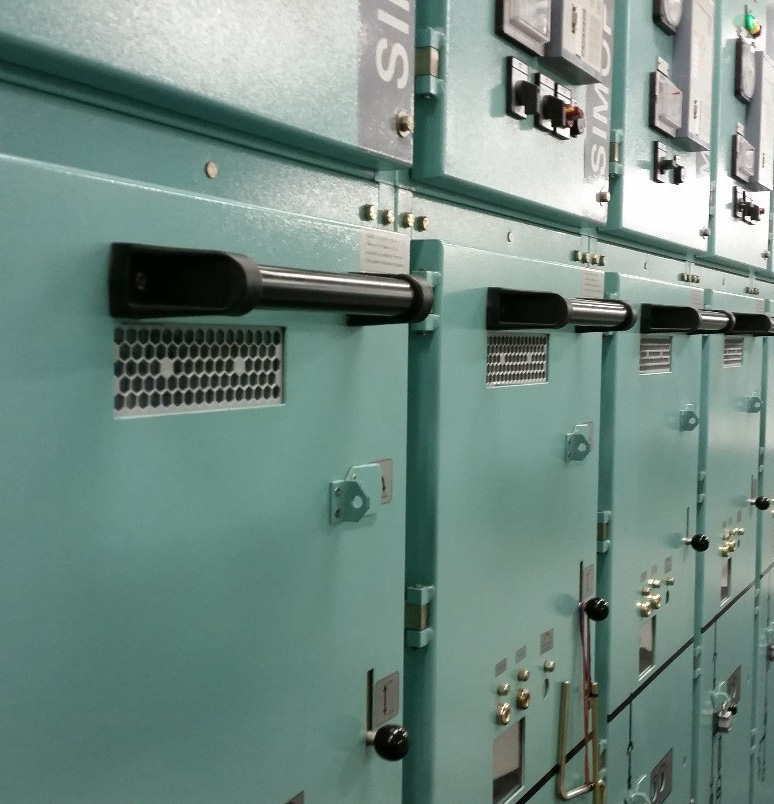
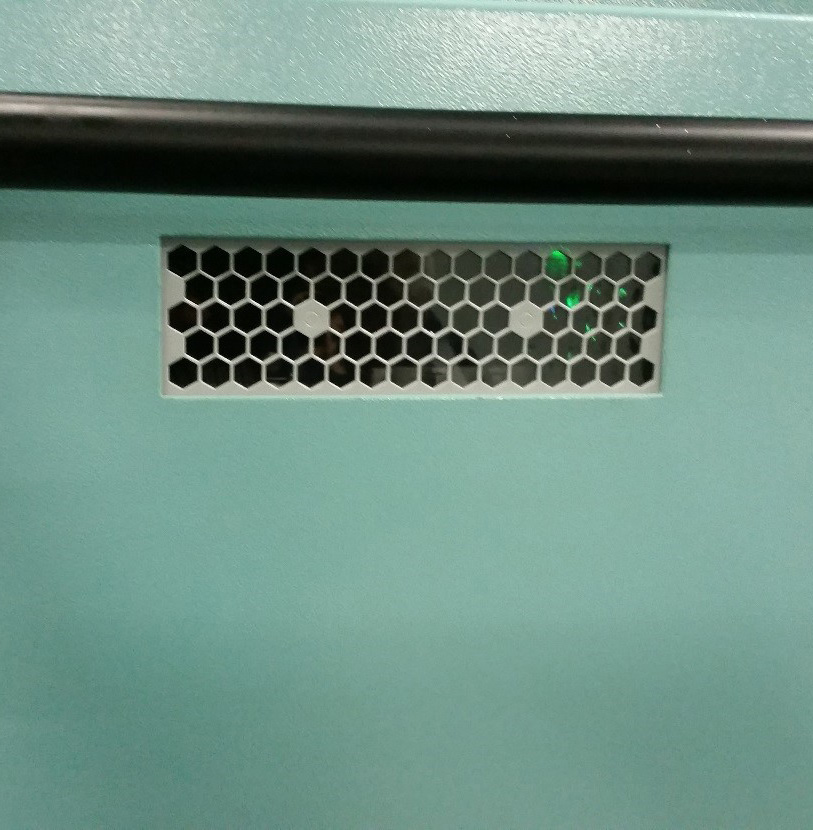
The cost-benefit of performing the infrared inspections was phenomenal. The total
inspection time was reduced to one person inspecting all equipment over three to
five days. Over 90% of the inspection labor hours were eliminated by implementing
the IRISS FlexIR Custom Windows. It’s estimated that the IR window investment was
paid for within two inspection cycles after installation.