by Dominique Capili, Spectrum Scientific Corporation (An IRISS Distributor)
Overview
A prominent geothermal energy producer in the Philippines has become a leader
through the successful development and operation of numerous energy projects.
Since 1983, the company has successfully developed, financed, built and operated
seven geothermal steam fields for both wet and dry steam and also owns and
operates eleven geothermal power plants. Using the company’s expertise, they seek
continual improvements to ensure the safe and efficient construction and operation
of current and future power plants.
Temperature plays a key role in the everyday maintenance and condition monitoring
processes of a power plant. Temperature is the first parameter that is monitored to
measure the health of the equipment. Maintenance professionals have been
integrating thermography into their maintenance programs to increase efficiency and
determine if the equipment is still within the allowable temperatures set by its OEM
during operation. For an effective thermographic survey, one must have a direct line of
sight exposing the surface to be measured. Previously, for an electrical inspection of a
4160-volt metal-clad switchgear, the inspector had to remove eight bolts, carefully lift
and remove the heavy steel back cover away from the panel and then later inspect it
with an infrared camera. This procedure is time-consuming, troublesome and most of
all, dangerous due to the increased risk of producing an arc flash.
Thermography is used in maintenance programs because of three unique
characteristics:
- It can be performed at a safe distance away from the hazards surrounding the
equipment without compromising the safety of the plant personnel. - Two-dimensional inspections enable the visualization of the changes in heat
patterns on the surface of the equipment. This assists in the interpretation of
“what” or “where” a fault may occur. - Real-time visualization of thermal patterns helps analyze the equipment in its
fully energized state.
Infrared polymer windows, when mounted on fully energized equipment, allow
infrared energy to pass through making thermography inspections safe and in
compliance with NFPA/CSA/OSHA or any other local safety regulations.
Inspections are completed without equipment shutdown providing real-time data
assessments of a facility’s critical assets.
Installation
Over a period of three weeks, twenty-seven (27) IRISS Infrared Windows were
recently installed with no lost time or accidents. Due to safety concerns, the previous
site survey and visual inspection were limited to external surface temperature
measurement and visual inspection of panels with the absence of opening any doors
or covers. The preliminary installation design was based on shop drawings that
determined the quantity, size and specifications of the infrared windows needed.
During the scheduled shutdown, actual visual inspections and de-energized openings
of panels were conducted to identify and verify which components would be a main
priority for the infrared inspections. Several window sizes and exact locations were
changed once the open panel inspections were performed.
In total, twenty-two (22) CAP-C-6 and five (5) CAP-C-4 windows were installed on
twelve (12) 4.16kV panels and fifteen (15) 13.8kV panels, generators and
transformers.
Installation Photos
Pre-Installation
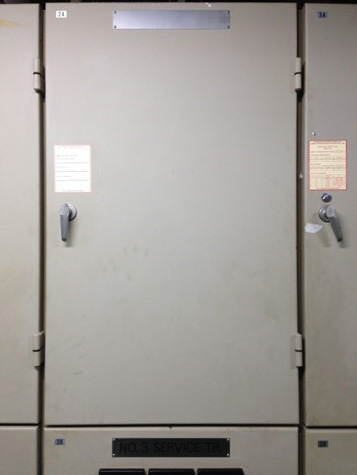
Post-Installation
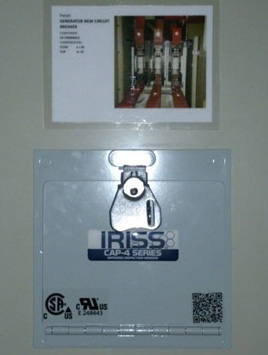
Step 1: Lay Out
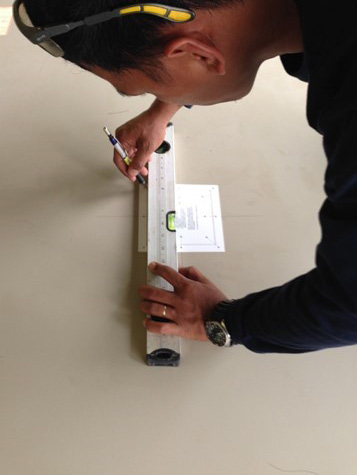
Step 2: Cutting & Drilling
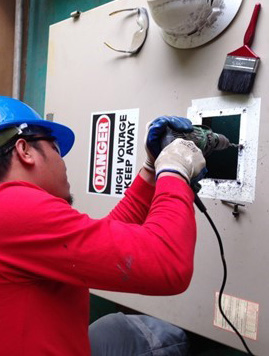
Step 3: Touchup Painting
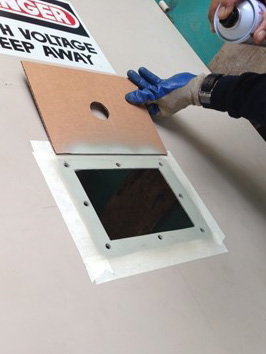
Step 4: Mounting
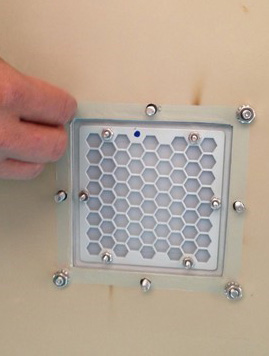
Equipment Testing
The last few days were allocated for bench testing, simulation of readings using
multiple OEM IR camera types and training of personnel. The simulation of readings
using the various camera types and a Black Body temperature source through the
IRISS infrared polymer windows measured distance-corrected ambient temperature,
emissivity usage values and parameter settings on the respective devices.
Bench Testing
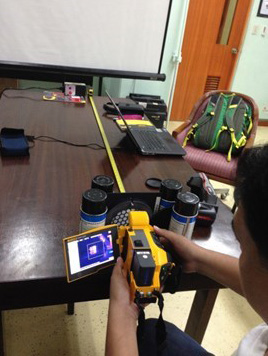
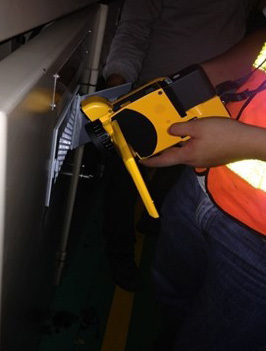
Black Body Simulation
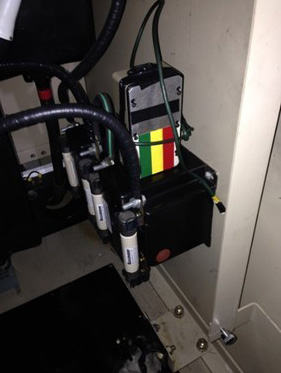
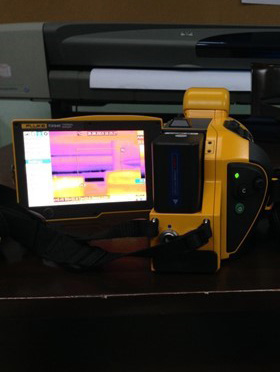
Where possible, connections were taped with known emissivity insulating tape. In
this way, more accurate temperature readings can be taken of the target potential
hot spots.
Emissivity Tape Mounting
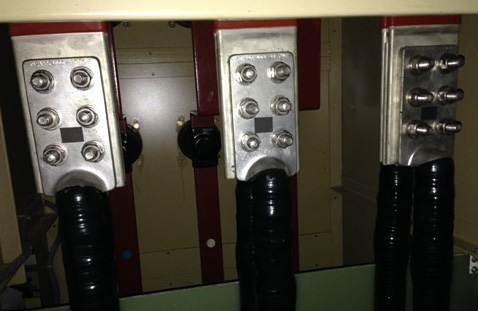
As an opaque polymer optic was used on this project, digital photos were taken,
laminated and then placed adjacent to the respective inspection window. Target
locations for IR inspection were included on the digital image as well as the proper
transmission rate for each camera type that might be used by the inspector. In this
way, the future IR inspector will have a better idea of what they are looking at with the
IR image and it will ensure consistent and accurate temperature data collection
methods.
Labelling
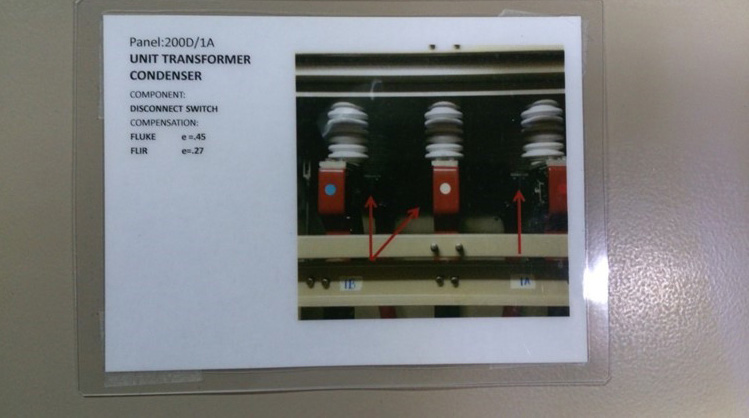
Conclusion
Since the initial IR Window installation, the program has helped the inspection team
decrease the time required to conduct inspections as it does not require a “hot
work” permit and can be done by a single person with no need for special personal
protective equipment (PPE). As of publication of this document, they have not found
any serious faults but have observed some slight temperature rise on some assets
that are being trended and monitored for future change. Plans are being made to
expand the use of IR windows on other equipment at this site as well as other
power plants owned by the power producer.